Metals have always been an integral part of human civilization due to their robust and durable nature. Though welding was earlier used for making daily-purpose items such as ornaments, utensils, and furniture, it was the Industrial Revolution that gave a broader direction to welding.
Under this revolution emerged the necessity of understanding different types of welding processes and their applications. Today, welding is being used in almost all fields, right from auto parts to electronic components, from manufacturing to construction, and from microchips to skyscrapers.
This article provides an overview of welding, different types of welding processes, along with their pros, cons, and applications.
[PS: We also have a guide on Different Types of Welding Joints & Their Applications]
What is Welding?
Welding can be referred to as a process of joining two materials, specifically metals, by melting and fusing them. It involves melting the workpieces either by applying heat or pressure or by filling the gap with a filler material.
When the heat source is applied to the joint area, the temperature of the metals rises, thereby melting them. This heat can be generated through gas flames, lasers, or electric arcs, depending on the welding methods to be used.
As the metals start melting, the joint can be filled with a filler material, which may be in the form of an electrode or wire.
Welding has been used since ancient times to create weapons, utensils, ornaments, and furniture. Ancient welders used brazing and forge welding to fuse various metals such as iron, bronze, or gold to be used in different areas.
But with advancements in technology, welding found its way into transportation, construction, manufacturing, robotics, and aerospace industries. Today, there are a lot of welding methods that can be employed according to the metals to be joined.
Types of Welding Processes and Their Applications
Here’s a list of various types of welding processes and their applications.
1) Metal Inert Gas (MIG) Welding
Metal inert gas welding, also known as gas metal arc welding, is one of the different types of welding processes. Since it is a fully or semi-automatic process, it uses direct current or alternating current from the power supply. It is a metal-bonding process that can bond and shape even dissimilar metals.
In this process, the welding gun is filled with a filler wire that acts as an electrode. When the welding gun and workpiece metals come into contact, an electric arc is formed that melts the filler material which leads to the joining of the metals.
Also, a shielding gas is supplied in the gun to prevent any contamination with any inert gas, such as argon or a mixture of argon and carbon dioxide.
Pros:
- It is the easiest welding technique to learn for beginning welders.
- It can weld thick and thin metal sections easily, including Aluminium, Stainless Steel, Carbon Steel, and other alloys.
- It offers high-quality welds at a good speed.
- It has good mechanical properties, due to which welds can be produced with minimal spatter.
Cons:
- It is not suitable for outside welding as it is sensitive to various external factors.
- It makes the overall structure weak due to porous and dross quality.
- It does not prevent metal from rust or slag.
Applications:
- It is used in the automobile industry for wielding heavier metals.
- It plays a great role in preparing and assembling railroad tracks.
- It is popular for welding pipes to run the water system or sewage of the cities smoothly.
- It can be used in various other sectors, including construction and aerospace industries.
2) Shielded Metal Arc (Stick) Welding
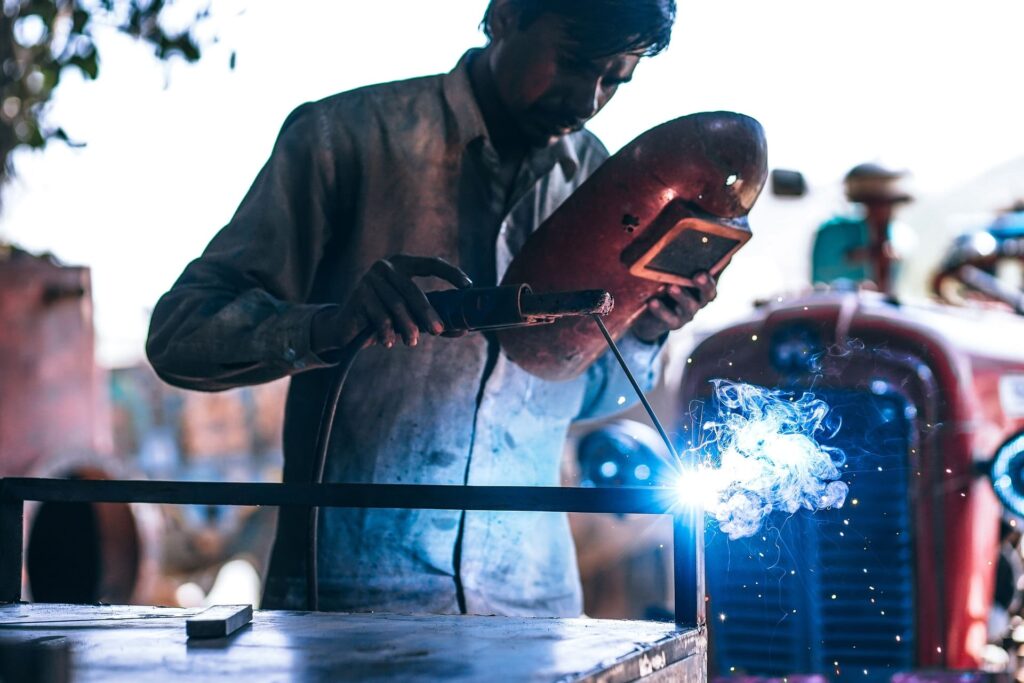
Shielded metal arc welding, also known as stick welding or flux-shielded arc welding, is one of the simplest and basic types of welding process. Since it is a manual process that uses a flux-covered electrode along with a continuous power supply (either alternating or direct current), it is also known as manual metal arc welding.
In this process, a consumable electrode, usually replaceable, acts as a filler material. An arc is generated when the electric current comes in contact with the metal workpieces. The heat of this arc melts the filler material, leading to weld production.
The vapors emitted from the electrodes form a shielding gas that prevents the weld area from oxidation. Further, after cooling, the flux turns into slag that needs to be chipped off.
Pros:
- It is cost-effective.
- It has simple and easy operability.
- It is compatible with various metals such as Iron, Steel, Nickel, Copper, and Aluminium.
Cons:
- The welds produced are not of the best quality.
- It is a difficult process to master on.
- The electrodes used in stick welding need to be replaced frequently.
- It requires cleanup because of the spatter produced.
Applications:
- Since the equipment used in the process is portable, stick welding can be used for completing small and large tasks even in remote locations.
- The electrodes are wind-resistant due to which this process is opted at outdoor construction sites.
- It is commonly used to repair farm equipment because it can weld rusted, dirty, and painted metals.
3) Tungsten Inert Gas (TIG) Welding
Tungsten inert gas welding, commonly known as gas tungsten arc welding, is one of the different types of welding processes. Though it is among the advanced processes, it is a manual arc welding process usually applied to weld heavy metals. The source of the electric current can be both alternating current and direct current.
It requires two hands to obtain strong welds through TIG: one for holding the TIG torch while the other for feeding the filler rod. It uses an electrode made of non-consumable tungsten to spark an arc between the metal workpieces.
With the help of a TIG torch, heat is produced, and an arc is generated which quickly joins the metals. During this welding process, a shielding gas, usually argon or helium, is continuously supplied to protect the welded area from oxidation or contamination.
Pros:
- It offers high-quality and clean welds with great precision.
- It can be used to weld thin sections of various metals, including Stainless Steel, Magnesium, Aluminium, and Nickel.
- It can be done without any filler metal.
- No cleanup is needed because TIG does not create any weld spatter.
- It can easily adjust the flow of gas and current according to specific requirements.
Cons:
- It is a complicated welding technique and can only be performed by experts.
- Since it is a slow process, it is time-consuming.
- It leads to greater production costs.
Applications:
- It is used in the aerospace industry to fabricate various heavy components such as fuel tanks, engine parts, and aircraft frames.
- It is used in the automotive sector to produce body panels and exhaust systems.
4) Flux-cored Arc Welding (FCAW)
Similar to metal inert gas welding (MIG), the flux-cored arc welding (FCAW) process is a fully or semi-automatic welding process that uses a continuous electrode, filler metal, and constant power supply (alternating as well as direct current). Among different types of flux-cored arc welding are gas-shielded and self-shielded FCAW.
In this process, there is a tube-shaped wire that acts as a flux that creates a gas shielding around the weld area. This gas is supplied from an external point using a high-pressure gas cylinder, saving the weld pool from oxidation. The weld area is also shielded through slag formed during the melting process of flux.
When the external gas is not provided, the welding uses the flux-cored electrode to protect the weld area. This electrode emits gas which converts into slag to prevent the metal from being contaminated. Further, the process offers additional alloying elements to enhance the existing mechanical properties of the metals to be welded.
Pros:
- It is suitable for both outdoor and indoor use.
- FCAW is cost-effective as external gas is not needed.
- It can be used for welding heavier and thicker metals.
- It offers high penetration and deposition rates.
Cons:
- Cleanup is required as a little debris is left after the completion of the process.
- Due to high heat input, this process is not suitable for welding thin metals.
- It generates relatively more smoke as compared to other welding processes.
- The welds produced are of low quality.
Applications:
- As it is adaptable to different positions, it is highly recommended in pipeline construction, shipbuilding, and repair work.
5) Gas Welding
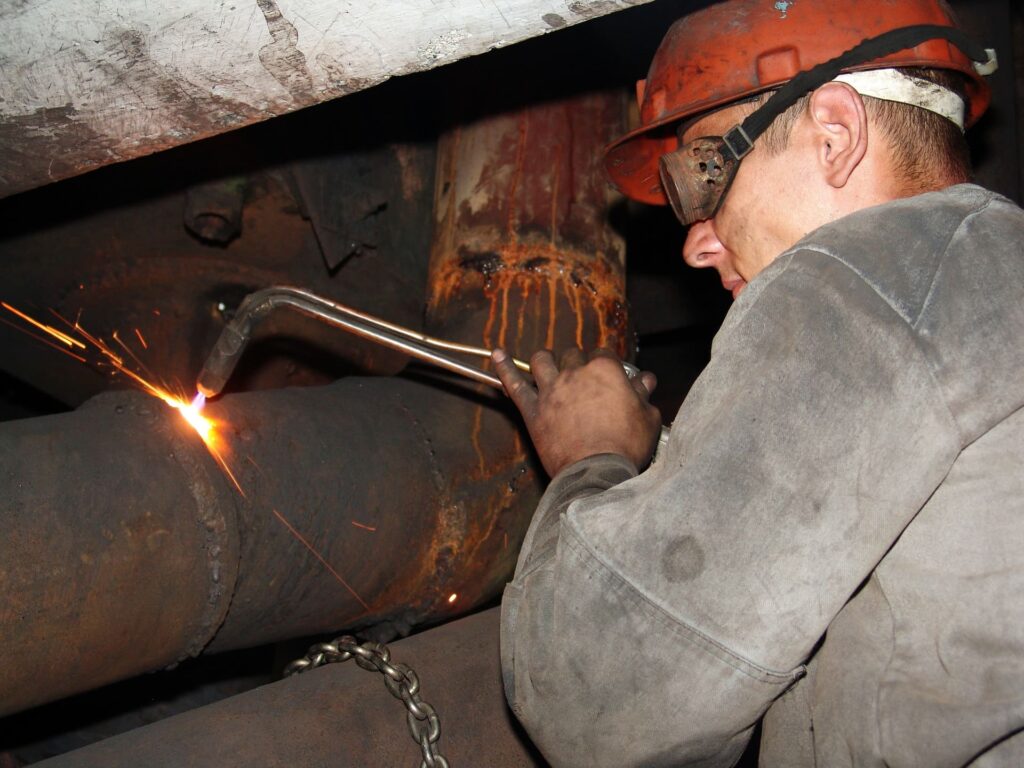
Also known as oxy-fuel welding, gas welding is one of the popular welding processes developed by Edmond Fouche and Charles Picard in 1903. It works on the principle of combustion of oxygen with fuel gases such as acetylene, butane, hydrogen, and propane. The filler metal is optional in gas welding.
In this process, heat is generated from a concentrated flame which is controlled by a blowpipe or hand-held torch. This flame can be an oxidizing flame, carburizing flame, or neutral flame. The oxygen and fuel gases are mixed in equal proportion inside the torch.
When the temperature rises to 3200 degrees Celsius, the torch is brought close to the metal workpiece, which results in the melting and joining of the metals. The intensity of the flame can be controlled with a pressure regulator.
Pros:
- The pressurized gas is filled in a handy cylinder, which makes the welding equipment portable.
- It is cost-effective in terms of maintenance and repairs.
- It is an easy-to-learn process and can be conducted even by a novice.
- It is used to weld materials like mild steel and braze other materials like Copper, Stainless Steel, Brass, and Aluminium.
Cons:
- Owing to the rate of metal joining, the speed of the gas welding process is low.
- It is not suitable for thicker sheet metals.
- It does not create the flux shield around the weld lines.
- Welds produced have rough appearance and require additional finishing.
- It cannot weld reactive materials such as zirconium, titanium, and high-speed steel.
Applications:
- Gas welding helps to join damaged parts due to which it is readily used for automobile and aircraft repairs.
- Since it can weld thin metals, it is used to fabricate sheet metals.
- It can effectively melt and join high-carbon steel.
Other Types of Welding Process
Apart from the above-listed processes, there are some other less-known yet powerful types of welding processes, too. These include forge welding, resistance welding, plasma arc welding, atomic hydrogen welding, electron beam welding, submerged arc welding, carbon arc welding, and electro-slag welding.
Below, we discuss these different types of welding processes and their applications.
1) Forge Welding
The oldest welding process is forge welding in which small iron metal pieces are heated and then hammered. After hammering, the final weld is allowed to cool down into the desired shape.
2) Resistance Welding
In resistance welding, metals are joined by applying pressure and passing current. The heat is generated through electric resistance which helps to melt and fuse the metals. Some of the common resistance welding types include projection welding, seam welding, and spot welding.
3) Plasma Arc Welding
Plasma arc welding, similar to tungsten inert gas welding, is used in various welding projects, such as the aircraft industry, that involve working at higher temperatures. In this process, an electric current is passed through a nozzle to form a smaller arc.
A shielding gas is also supplied to prevent any contamination. Though it is an expensive technique, the final welds produced are smooth and clean.
4) Atomic Hydrogen Welding
The atomic hydrogen welding process was developed by Irving Langmuir, an American chemist who discovered atomic hydrogen. Though it is the older version of metal inert gas (MIG) welding, it is still used in the tungsten welding process.
The two metal electrodes made of tungsten are placed in the hydrogen atmosphere, which, when heated, can heat up to 3000 degrees Celsius.
5) Electron Beam Welding
Electron beam welding works on the principle of converting kinetic energy into thermal energy. A ray of electrons is fired to the metals under a vacuum condition which helps in melting the sheets to weld the metals properly.
It is a complex process and is usually used to make bimetal saw blades, aerospace components, and transmission assemblies.
6) Submerged Arc Welding
Submerged arc welding is one of the less frequently used arc welding processes. It is both a fully as well as semi-automatic process which makes it quick to join metals efficiently. Here, the flux, made up of granular fusible material, acts as an electrode to shield the welded area from infrared radiation and UV light.
In this process, strong welds are produced with greater penetration and minimal spatter.
7) Carbon Arc Welding
In carbon arc welding, the metals are joined by applying temperatures more than 300 degrees Celsius. The heat generates an arc between metal workpieces and electrodes. Though it was popular in ancient times, it has been replaced by the twin-carbon arc welding process in recent decades.
8) Electro-slag Welding
One of the most effective and quickest welding processes is electro-slag welding. It is a vertical process that can significantly weld metal workpieces of thickness between 25mm to 300mm. In this process, heat is generated via an electric supply (either alternating current or direct current) to bond heavy metal pieces usually used in industrial equipment.
The tool gun has copper water holders that prevent slag from being liquified from seeping into areas other than the welded area.
Key Takeaways
In this article, we have discussed various types of welding processes and their applications. Each of these processes has its advantages, disadvantages, as well as limitations. Thus, it depends on the type and thickness of materials, surface, welding purpose, desired weld quality, and environmental conditions under which the welding is being conducted.